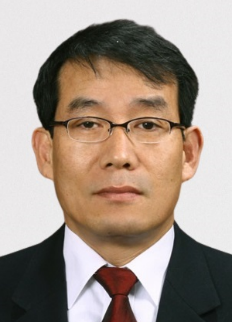
Speaker
Jong-Kil Kim
Professor, Hanyang University / Institute of Engineering and Technology
......
Title: Overview of Solid-Liquid Separation Process Technology and Automatic Coastal Erosion Restoration Technology Using Sediment Settling Process
Abstract:
To separate materials in which liquids and solids are mixed, various separation techniques are applied based on the size and characteristics of the solid particles in the liquid. Solid-liquid separation technology is utilized in almost every aspect of our lives, making it essential to understand the fundamental concepts and applications of these techniques. In this presentation, we aim to introduce the basics of solid-liquid separation processes. Additionally, we will explore how solid-liquid separation technology can be applied to address the increasingly severe issue of coastal erosion, exacerbated by climate change. Specifically, we will introduce an automatic coastal erosion restoration technology that reduces wave energy to accelerate the settling of sediments and enhance the natural restoration of eroded coasts. This innovative approach leverages wave energy reduction and sediment deposition to support sustainable coastal management.
Short Bio:
- PhD: HanYang University (Nano-Material Chemistry)
- MBA: Korea University (Technology Transfer)
- Director, Professor: National Univ of Mumbai, India
- Chairman, Professor: Asia Pacific Eco-Tech Alliance
- Professor: Hanyang University / Institute of Engineering and Technology
- Chairman: Powder Technology section of the Korea Chemical Engineering Association
- Chairman: Korean Council of Industrial Professors (Chemical field)
- Vice Chairman: Korean Filtration and Separation Society
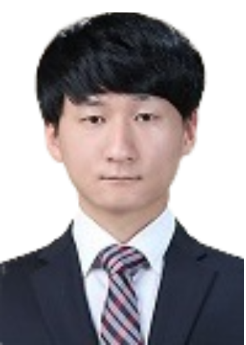
Speaker
Gyeongju Seo
Clean and Science
......
Title: Basic Information on Chemical Filters in Air Filtration Application
Abstract:
Chemical Filters are the most important filters in the modern filtration industries. They are widely used to remove harmful gaseous contaminants such as ozone, nitrogen dioxide, sulfur dioxide and carbon monoxide. Activated carbons are commonly adapted for this application due to effectiveness and cost benefits. The most of time, these activated carbons are impregnated with various chemical materials for improving absorbing performance for a targeting a specific harmful gaseous contaminant. The ion exchange resin is getting popular for absorbing gaseous contaminants.
Short Bio:
Received BS and MS in advanced materials from Chonnam National University, Gwangju, Korea.
Currently he is a manager of Clean and Science R&D Dept developing chemical filters.
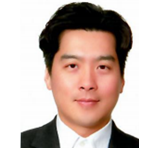
Speaker
Sang-gu Lee
Principal Scientist, Korea Conformity Laboratories
......
Title: Airborne Microorganism Antibacterial/Antiviral Hybrid Filter Technology and Evaluation Method to Prevent Indoor Air Quality Infections
Abstract:
Due to the COVID-19 issue, antibacterial/antiviral technology to prevent indoor air quality infections has developed rapidly, and large companies such as Samsung and LG are selling related products. This presentation aims to help students learn related concepts by explaining the necessity, principles, and certification methods of antibacterial/antiviral technology.
Short Bio:
Dr. Lee Sang-gu majored in aerosol application in the Department of Mechanical Engineering at Yonsei University, where he conducted research on nano sensors and antibacterial devices. He also developed air purifier element technology at the LG Electronics CTO Research Institute. Currently, he is working at Korea Conformity Laboratories, focusing on test development and leading national R&D projects related to environmental air quality sensors and air purification devices.
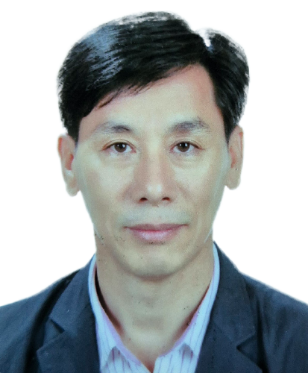
Speaker
KwanSoo Ha
Vice Chair of the Korea Ozone UV Association / BioZone Scientific Korea Co., Ltd.
......
Title: Understanding the Wavelengths of UV and the UV Dosage Required for 99.9% Destruction Various Organisms
Abstract:
In the ï¬ght against the coronavirus disease 2019 (COVID-19) pandemic, an old weapon has re-emerged.
More than a century after Niels Finsen won the 1903 Nobel Prize for discovering that ultraviolet (UV) light could kill germs. UV light is surging in popularity as a method for disinfecting hospital rooms and other public spaces.
Pathogens have evolved, but our tools to clean the environment have not it. We need a new tool to ï¬ght them, not just a mop and bucket.
Short Bio:
He is currently Vice Chair of the Korea Ozone UV Association / BioZone Scientific Korea Co., Ltd.